煤气发生炉工作原理是以煤为原料生产煤气,固体原料煤从炉顶部加入,随煤气炉的运行向下移动,在与从炉底进入的气化剂(空气、蒸汽)逆流相遇的同时,受炉底燃料层高温气体加热,发生物理、化学反应,产生煤气。这样在煤气发生炉中形成了几个区域,一般我们称为“层”。按照煤气发生炉内气化过程进行的程序,可以将发生炉内部分为六层。1)灰渣层;2)氧化层(又称火层);3)还原层;4)干馏层;5)干燥层;6)空层;其中氧化层和还原层又统称为反应层,干馏层和干燥层又统称为煤料准备层。
(1)灰渣层:
煤燃烧后产生灰渣,形成灰渣层,它在发生炉的*下部,覆盖在炉篦子之上。其主要作用为:
a保护炉篦和风帽,使它们不被氧化层的高温烧坏;
b预热气化剂,气化剂从炉底进入后,首先经过灰渣层进行热交换,使灰渣层温度**,气化剂温度升高。
c灰渣层还起了布风作用,使进入的气化剂在炉膛内尽量均匀分布。
(2)氧化层:
也称为燃烧层(火层)。从灰渣中升上来的气化剂中的氧与碳发生剧烈的燃烧而生成二氧化碳,并放出大量的热量。它是气化过程中的主要区域之一,其主要反应是:
C+O2→CO2
氧化层的高度一般为所有燃料块度的3-4倍,一般为200毫米。气化层的温度一般要小于煤的灰熔点.
(3)还原层:
在氧化层的上面是还原层。赤热的碳具有很强的夺取氧化物中的氧而与之化合的本领,所以在还原层中,二氧化碳和水蒸气被碳还原成一氧化碳和氢气。这一层也因此而得名,称为还原层,其主要反应为:
CO2+C→2CO
H2O+C→H2+CO
2H2O+C→CO2+2H2
(4)干馏层:
就是把煤中的挥发份,焦油等物质经过加热后所产生的CmHm化合物分离出来,然后再进入还原进行化学反应。
(5)干燥层:
干燥层位于干馏层上面,也即是燃料的面层,主要是把煤中的水发蒸发即可。
(6)空层:
空层即燃料层上部,炉体内的自由区,其主要作用是汇集煤气。
富氧气化实施依据
根据混合煤气发生炉内进行的化学反应,其主要反应发生在气化层,即氧化层和还原层。煤首先在氧化层燃烧产生大量的热,然后以产生的热量供给还原层促进还原反应的发,如果没有充足的热量则还原反应很难发生。燃烧即是碳与氧发生是的氧化反应,生成CO2,在由CO2、水蒸气和碳发生还原反应生成CO、H2等可燃性气体,其中还原反应需要大量的热,如果热量不足则还原反应就不能进行。
在还原层,高温蒸汽H2O裂解成H2与CO要大量吸热,CO2还原成CO要大量吸热,提高炉温,需增加鼓风量,增加含量为78%的N2;提高煤气热值,与鼓风量的增加是一对主要矛盾,蒸汽量增大,炉子温度要**,鼓风量增大,N2要大量进炉,要减少风量,又要提高煤气热值,矛盾突出。富氧燃烧既能提高炉温,又大量减少N2(空气)的进风量,一举两得地解决了技术难关。
与传统空气-水蒸气制取是煤气相比,富氧煤气采用富氧空气与水的混合物作为气化剂,提高了气化剂中氧的浓度,加剧了碳的氧化反应,炉温升高,使气化速度加快,提高了气化强度和气化效率;同时煤气中惰性组分下降,煤气热值得到了有效的提高。
采取富氧空气制取煤气时,为了**氧化层温度防止*作温度过高,热损增大,造成炉渣溶结而影响炉料的透气性,在鼓风中需要增加水蒸汽的供入量,利用碳和水蒸汽的吸热反应,**气化层的温度。水蒸气象氮气那样将热量从氧化层带到还原层,提高了氧化层热量利用率和还原层的温度。随着富氧空气中氧浓度的增加,则燃烧速度加快,单位时间和空间内产生了更多的热量和CO2, 同时气化剂中水蒸气的含量提高都为还原反应做了**的准备。在还原层的主要反应是:
CO2+C→2CO -162.4 kJ/mol
H2O+C→H2+CO -188.8 kJ/mol
2H2O+C→CO2+2H2-75.2 kJ/mol
由此可见,增加反应物浓度、提高反应温度能有效的促进还原层反应向右进行,提高气化效率。
提高燃料层温度,增加煤气热值
根据阿累尼乌斯定律,燃烧反应速度与温度成指数关系,因此温度对燃烧过程有着极其显著的影响,温度高,着火快,燃烧速度快,燃烧过程进行的更加剧烈,燃烧也易于趋向**。
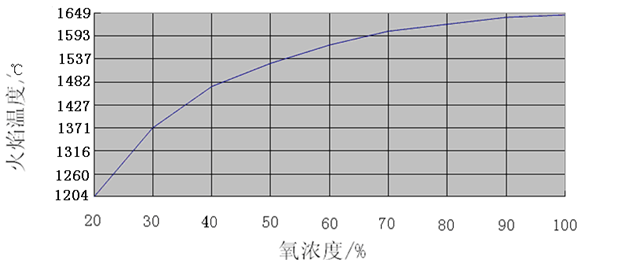
图3 氧浓度与火焰温度的关系
用燃料理论燃烧温度计算公式来简单地做个计算对比,更能说明问题。理论燃烧温度计算公式如下:
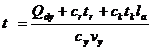
(4-1)
式中:

——燃料低位发热量,Kj/Kg;

——燃烧产物,空气,燃料的热容量;

——燃料,空气的温度 ℃;

——燃料生成的烟气量,m3/Kg;

——不同过量空气系数时的燃料单位空气耗量,m3/Kg。
设烟气量=α,其中α为烟气生成系数,因此富氧前理论燃烧温度为:
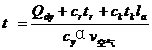
(4-2)
富氧后的理论燃烧温度为:
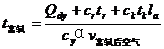
(4-3)
(2)式比上(1)式可得,
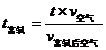
(4-4)
由此可以看出,富氧后减少烟气量,理论燃烧温度显著提高提高。混合煤气发生炉中的有效成分(CO+H2)的含量主要取决于CO2还原反应和水蒸汽分解反应的进行,即:
CO2+C→2CO -162.4 kJ/mol
H2O+C→H2+CO -188.8 kJ/mol
以上两反应均为吸热反应,因而燃烧温度的提高有利于CO和H2平衡浓度的增加。而且在通常的发生炉*作温度下,上述两反应的反应速度均处于动力学控制区范围,提高反应温度有利于CO2、H2的还原反应向右进行。当采用富氧气化时随着气化剂中氧浓度的提高,反应温度随之提高,只要增加蒸汽量,就可以在**的温度范围内进行*作;采用普通空气助燃,其中79%的N2不参与燃烧而且要带着大量的热,还会阻碍气化反应的进行,富氧气化可以减少助燃风中的N2量,煤气中N2浓度也随之下降,可燃气体比例增加,此时,煤气的热值得到了有效的提高。
加快气化反应速度,提高气化强度
燃烧过程是一个复杂的受物理化学因素影响的多相燃烧过程,在此过程中既发生燃烧化学反应,又发生质量和热量的传递、动量和能量的交换。煤种可燃物主要是碳,而且燃烧时间也相对较长,所以碳的燃烧快慢是整个过程的燃烧关键,关系着整个气化反应过程。
气化反应速度取决于碳的**氧化反应,这是一个由外扩散控制的反应,即是说影响燃烧速度的决定因素是物理混合条件,即氧气的扩散速率,提高气化剂中氧气的浓度,增加氧气扩散速率,保证碳表面有足够的氧气维持碳的快速燃烧,碳的氧化反应加剧,炉温随之上升,使氧化反应速度加快,单位时间释放的热量亦相应增加,从而给还原反应提供了充足的热量,它可使单位时间、单位炉截面上气化碳量增加,也就是提高了气化强度和气化效率。
3.3 **灰渣含碳量,提高碳利用率
煤气发生炉原料的带出物损失是由于气流在料层中及发生炉炉顶空间的流动而引起的,当气流速度大于固体颗粒的极限沉降速度时,颗粒即被气流带出,造成碳的损失,气流速度愈大,则带出损失就愈大。富氧气化工艺通过氧含量的增加相对**气流速度,可进一步减少带出物;富氧气体浓度高、反应快,加快了碳的燃烧速度,缩短了燃烧时间,在有效的时间内促进氧化层碳的**燃烧,**灰渣含碳量,提高碳的利用率。
3.4扩大煤种适用范围
富氧气化后,随着气流速度的**,对原料煤的机械强度和热稳定性要求**。高灰份、反应性差的煤通过氧含量的提高**可以应用于常用煤气发生炉,扩大煤种的使用范围。
(1)富氧气化后,其煤气成分出现一些变化,尤其是CO的成份**提高,而N 的成份**下降,说明采用富氧气化后炉内气化反应更加**,而空气中的N 吸入量**下降,但蒸汽消耗量也增加,饱和温度由原来的6O℃左右提高到68℃左右,致使富氧前后的蒸汽分解**下降,CO与未分解的蒸汽反应,使CO:和略有提高。但煤气热值提高了
482.6KJ/m ,接近7个百分点。
(2)由于采用富氧气化,煤气热值的提高,总鼓风量也有较大幅度的下降。富氧前供应熔化的平均总流量为1320m3/h,采用富氧气化后,平均总流量为1140m3/h,下降了180m3/h,而且熔化玻璃原料的温度**稳定,根据熔化情况,温度能很好控制,确保了熔化量380吨/天,这是单段炉无法做到的。
(3)由于鼓风量的下降,**了发生炉的炉底压力,这样就大大地减少了炉内煤粉的飞扬,烟道中烟灰及焦油**减少。烟道压力**,压力损失减少,对大窑后期的生产稳定起到保证作用,其潜在效益****。
(4)由于采用富氧气化,煤与氧气的接触面积增大,气化反应得到加强和**,使灰渣的残碳含量**下降。在富氧前,残碳含量居高不下,基本上在25%左右;富氧后,残碳含量基本上控制在19%左右,**了6个百分点。
(5)由于煤气热值的增加和残碳含量的**,煤的使用量**减少,每天日耗煤由富氧前的平均165吨下降到平均156吨,平均每天下降9吨。按到厂价450元/吨计,每天节约费用4050元